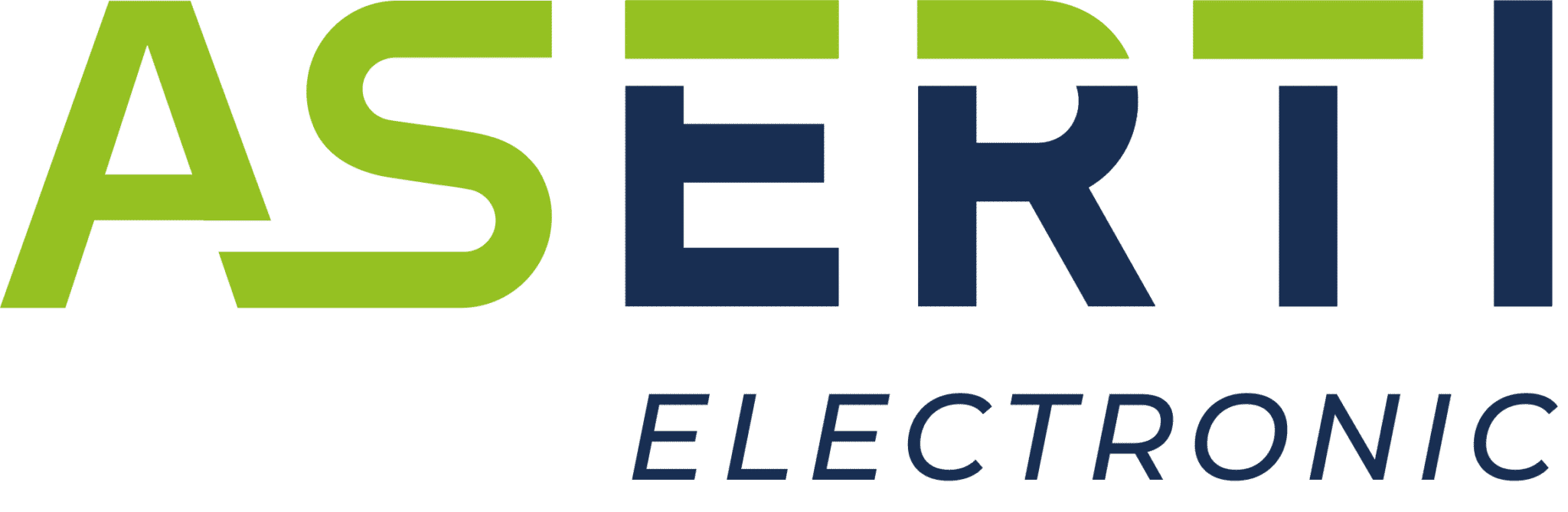
ASERTI Electronic
As a stakeholder in circular economy, ASERTI Electronic refurbishes and makes industrial equipment more reliable for a sustainable performance
View our PDF catalog
How can we help you?
They trust us
Repair Process for Your Electronic Equipment
The repair process in industrial electronics, particularly for critical machines and complex systems, includes several steps, from diagnosis to final testing, each step requiring precision and expertise. ASERTI stands out with a highly efficient, reliable, and comprehensive repair process, aiming to minimize downtime and ensure optimal machine performance.
Detailed Diagnostic Process
- ASERTI begins with an in-depth analysis to identify the cause of the problem. ASERTI goes beyond the initial symptoms by conducting thorough diagnostics to uncover underlying faults, helping to avoid recurring issues.
- Thanks to advanced diagnostic tools and highly skilled technicians, ASERTI can accurately detect errors and avoid misdiagnoses.
Use of Advanced Repair Techniques and Tools
- ASERTI invests in cutting-edge technology for the repair process, including sophisticated testing devices capable of simulating real-world operating conditions. This technology allows technicians to work precisely on sensitive and complex electronic systems from various brands and models.
- By using the most modern technologies, ASERTI is able to repair the most advanced and rare industrial electronic systems, setting it apart from competitors with more limited capabilities.
Use of High-Quality Replacement Parts
- During the repair, ASERTI uses high-quality replacement parts. The company maintains close relationships with suppliers to ensure the quality, reliability, and performance of the parts used, which are critical in industrial applications.
- The use of high-quality components increases the longevity and reliability of the repaired equipment, giving customers greater confidence in the durability of their systems after the repair.
Thorough Testing Before Delivery
- After the repair, ASERTI conducts extensive tests under simulated operating conditions. This step ensures that the equipment will operate optimally once installed at the customer’s facility.
- ASERTI’s commitment to rigorous post-repair testing minimizes unexpected failures and ensures that the equipment is fully functional upon return, a standard many competitors cannot achieve.
Fast Turnaround Times
- Since downtime is costly, ASERTI has optimized its repair processes to minimize turnaround times without compromising on quality. With efficient workflows and a highly skilled team, ASERTI can often return equipment more quickly than many other providers.
- Shorter repair times lead to reduced downtime for customers, making ASERTI the preferred choice for companies where every hour of downtime affects production and revenue.
Complete Documentation and Reporting
- ASERTI provides detailed documentation for each repair, including diagnostic results, repairs performed, parts replaced, and test results. This transparency helps customers understand the work done and facilitates smoother future maintenance.
- ASERTI’s commitment to transparency and record-keeping builds trust with customers, who can rely on clear documentation for asset management and future references.
Qualified and Experienced Technicians
- ASERTI technicians are not only highly qualified but also specialized in various brands and types of industrial electronics. This expertise allows them to work on a wide range of equipment, including rare or obsolete models.
- By investing in training and skill development, ASERTI ensures its clients benefit from highly skilled professionals capable of solving complex problems that other repair services may struggle with.
Environmental Awareness
- ASERTI places great importance on sustainability by focusing on repairs rather than replacements. This approach reduces waste and extends the life of equipment, aligning with environmentally responsible business practices.
- By supporting sustainable practices, ASERTI attracts customers looking for environmentally conscious partners, adding significant value beyond traditional repair services.
In summary, ASERTI’s repair process combines advanced diagnostics, high-quality replacement parts, fast turnaround times, thorough testing, and environmental awareness, all carried out by experienced technicians. This combination makes ASERTI a leader in the industrial electronics repair sector, offering unmatched reliability, efficiency, and added value to its clients.
Repair or Buy New: Why Repairing Electronics is Beneficial?
Minimizing Production Downtime
Repairs reduce machine downtime, allowing for a quick resumption of production and minimizing the impact on workflows and production.
Reducing Maintenance Budget
By repairing rather than replacing, customers can save on expensive new purchases and lower overall maintenance costs.
Extending Equipment Lifespan
Through proper repairs, the lifespan of machines can be significantly extended, delaying costly replacement purchases and increasing the long-term value of the equipment.
Improving Operational Efficiency
Repaired devices run more efficiently, ensuring optimal performance and potentially reducing energy consumption, leading to cost savings.
Increased Reliability and Performance
Thorough diagnostics and repairs ensure that equipment operates reliably, reducing the risk of unexpected failures or disruptions during operation.
Avoiding Unnecessary Replacement Purchases
Repairs offer a cost-effective alternative to complete replacements, especially for devices that are still in good condition but require repair to function optimally.
Compliance with Safety and Industry Standards
Ensuring that repaired equipment meets required safety and industry standards helps customers avoid penalties and ensures safe working conditions.
Sustainability and Environmental Responsibility
Repairing equipment instead of replacing it contributes to sustainability by reducing waste and minimizing the environmental impact of manufacturing new devices.